Progressing Cavity Pumps Definition and Advantages
A progressive cavity pump is positive displacement pump with two main pumping elements, the rotor and the stator. It is called PC pumps, Progressive Cavity Pump, Progressing Cavity pumps, Eccentric Screw pump, single screw pump, or Cavity pump. It transfers fluid by means of a rotor turning inside a stator with extra cavities where the fluid progress in a sequence of small, fixed shape, discrete cavities.
Due to its advantages because of this design, progressing cavity pumps have applications from fluid metering (Positive Displacement), pumping of viscous or shear-sensitive materials, to chemical transfers.
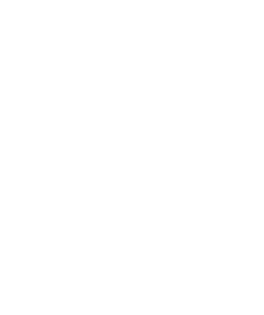
History of Progressing Cavity Pumps
Founder of the PCM company in 1932, René Moineau is the inventor of the Progressing cavity pump, also known as « Moineau pump ». It is common for equipment to be referred to by the specific manufacturer or product names. Hence names can vary from industry to industry and even regionally; examples include: Moineau (after the inventor, René Moineau). The original 4 Manufacturing licenses were issued to; MOYNO pump [Americas], Mono pump [UK, Europe], Gardier [Belgium] and PCM. All four original patent holders are now unified/owned by National Oilwell Varco (NOV)
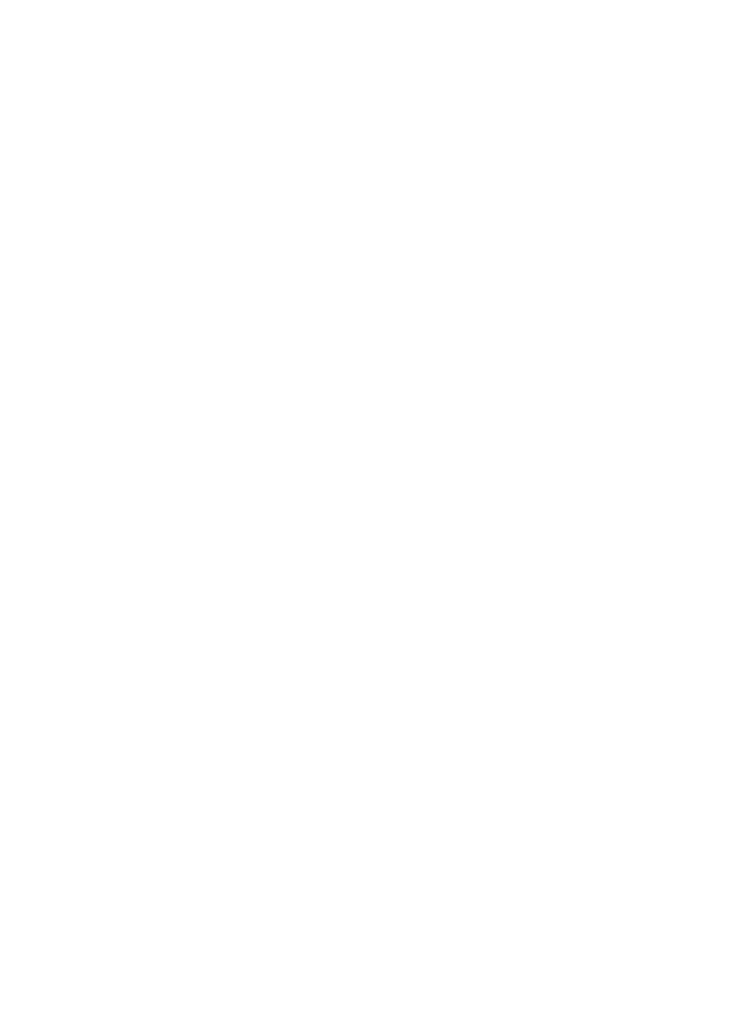
The Moineau principle has been utilized in many industries in a wide variety of applications since its licensing. It has
been used as a pump in just about every industry: chemical, coal, food, metalworking, mining, paper, petroleum,
textile, tobacco, and water and wastewater treatment. In the petroleum industry, the PC pump has been utilized as a
surface transfer pump for over 56 years.
In the mid – 1950’s, the progressing cavity pump principle was applied to hydraulic motor applications by reversing the
function of the progressing cavity pump. The device was then being moved by fluid instead of pumping fluid. With the
pump elements being driven by drilling mud or other fluids, it became the prime mover for drill motors. The Moineau
principle is now being widely used in the petroleum drilling industry.
Then in the early 1980’5, the PC pump was utilized as an artificial lift method in the petroleum industry. And very soon
in became know as an alternative pump to conventional lift methods and to establish a new marketplace for the PC
pump.
The pump is applied to artificial lift by attaching the pump elements to the tubing and rod string. The stator is run on
the end of the tubing, and the rotor is attached to the bottom of the rod string and landed in the stator. The rods and
rotor are rotated through a wellhead drive assembly that is designed to carry the weight of the rod and the fluid
column.
Currently, the PC pump is being widely used for lifting fluids from depths of 2000m, and deeper in oil and gas wells.
The progressing cavity pump offers to the petroleum industry a great number of advantages over traditional lift
equipment, of which the most important is lowering the cost per barrel lifted.
Advantages of Progressing Cavity Pumps
- High overall system energy efficiency, typically in the 55 to 75% range.
- Ability to produce high concentrations of sand or other produced solids.
- Ability to tolerate high percentages of free gas.
- No valves or reciprocating parts to clog, gas lock, or wear.
- Good resistance to abrasion.
- Low internal shear rates (limits fluid emulsification through agitation).
- Relatively low power costs and continuous power demand (prime mover capacity fully utilized).
- Relatively simple installation and operation.
- Generally low maintenance.
- Low profile surface equipment.
- Low surface noise levels.
Disadvantages of Progressive Cavity Pumps
- Limited production rates.
- Limited lift capacity. Note that the lift capacity of larger displacement PC pumps is typically much lower.
- Limited temperature capability, potential use to 350°F with special elastomers).
- Sensitivity to fluid environment (stator elastomer may swell or deteriorate on exposure to certain fluids, including well treatment fluids).
- Subject to low volumetric efficiency in wells producing substantial quantities of gas.
- Sucker rod strings may be susceptible to fatigue failures.
- Pump stator may sustain permanent damage if pumped dry for even short periods.
- Rod-string and tubing wear can be problematic in directional and horizontal wells.
- Most systems require the tubing to be pulled to replace the pump.
- Vibration problems may occur in high-speed applications.
- Paraffin control can be an issue in waxy crude applications.
- Lack of experience with system design, installation, and operation, especially in some areas.
Application of Progressing Cavity Pumps
WATER/WASTEWATER
Primary Treatment
- Sewage Lift Stations / Sewer Systems Headworks
- Primary Sedimentation
- Grit Removal
Secondary Treatment
- Secondary Sedimentation
Tertiary Treatment
- Nitrification
- Chemical Feed
- Tertiary Sedimentation
Solids Processing
- Thickening
- Conditioning
- Dewatering
OIL and Gas
- Multiphase Fluid Transfer
- Lease Automatic Custody Transfer (LACT)
- Produced Water
- Crude Oil Processing
- Drilling Mud Transfer
Food and Beverage
- Dairy
- Fruit and Vegetable Processing
- Meat Processing
- Brewing and Distilleries
- Confectionery
- Food Waste
Chemical
- Adhesives
- Slurries
- Chemical Metering
- Polymers
Mining
- Slurries
- Leaching / Neutralization
- Flocculants
Pulp and Paper
- Liquor
- Starch Slurry
- Cooked Starch
- Coating Kitchens
Other Applications
- Bio-Gas
- Pharmaceuticals
- Cosmetics
- Agriculture Industry
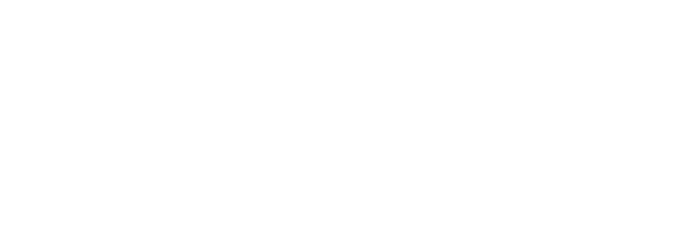
Maintanance and Operation for Progressing Cavity Pumps
- Replace the rotor for every two stators replaced on a pump.
- Used stators can often be reversed (flipped end for end) and reused.
- Check wear at the proper intervals and you can save the cost of a new rotor.
- If rotor wear is caught before the chrome plating is removed they can be re-chromed.
- Rotors worn past the chrome plating need to be replaced.
- It is rare for the rotor to be bent.
- Stators that are pitted, gouged or worn must be replaced.
- Use a a mild lubricant when installing the rotors into the stators.
- Flush product out of the pump while it is still in place to allow for easier and cleaner maintenance. Cover the suction and discharge flanges/opening to keep out foreign objects. Make notes of connections and orientations. Pictures are valuable tools in this case.
Pingback: 2000 SERIE MOYNO PUMPS | Pumps Center